
BUILDING TECHNOLOGY 05
"In pure architecture the smallest detail should have a meaning or serve a purpose."– Augustus W. N. Pugin

FLOOR SYSTEM AND ROOF SLAB SYSTEM
A Roof Slab is a reinforced concrete slab (in-situ or pre-cast) placed at the top of a structure onto which a water proofing or roofing membrane is installed, frequently as part of a reinforced concrete structural frame system. The Floor Slab, on the other hand, is a system of structural components that separates the stories of a building and a structural floor assembly between the beams and girders.
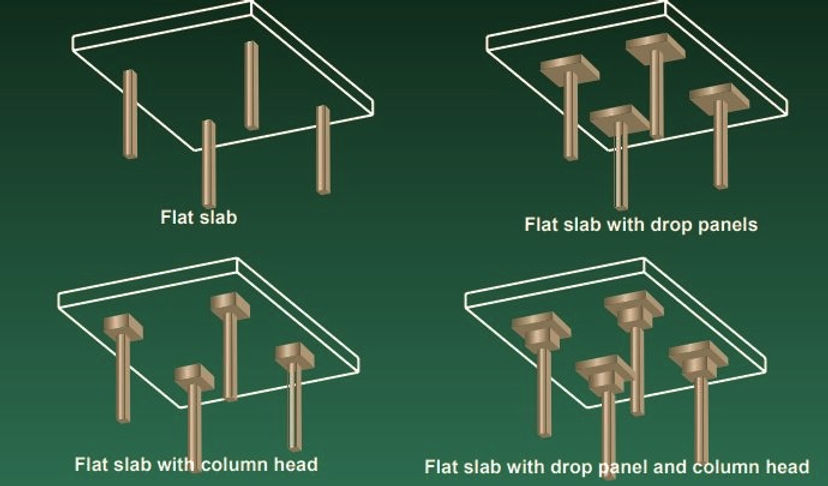
FLAT SLAB
A flat slab is a two-way reinforced concrete slab that usually does not have beams and girders, and the loads are transferred directly to the supporting concrete columns. The column tends to punch through the slab in Flat Slabs, which can be treated by : Using a DROP PANEL and a COLUMN CAPITAL in flat slab.Â
Uses of column heads :
• increase shear strength of slab
• reduce the moment in the slab by reducing the clear or effective span.Â
Uses of drop panels :
• increase shear strength of slab
• increase negative moment capacity of slab
• stiffen the slab and hence reduce deflection
![]() | ![]() | ![]() | ![]() | ![]() | ![]() |
---|
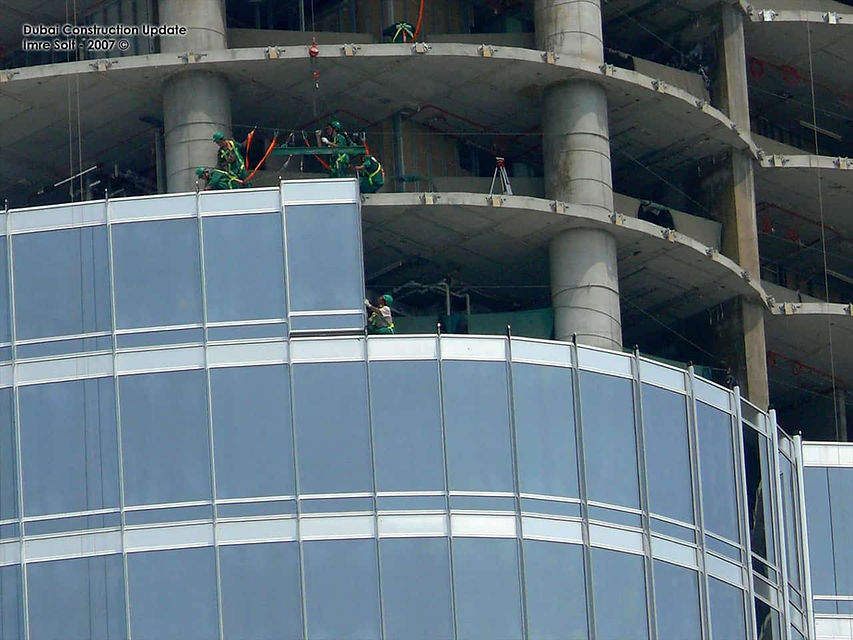
FLAT PLATE
A flat plate is a one-way or two-way system that is often supported directly on columns or load bearing walls. It is one of the most prevalent methods of creating floors. The flat plate floor's main characteristic is its uniform or nearly uniform thickness with a flat soffit that requires just minimal formwork and is straightforward to build.

RIBBED FLOOR SLAB
Ribbed slabs are made of large band beams that run between columns and are divided by narrow ribs that cross orthogonally. In most cases, the ribs and beams have the same depth. A thin topping slab completes the system. A one-way joist floor slab is composed of a series of small, reinforced concrete T beams connected by girders supported by the building column. T beams are joists formed by alternating the placement of steel pan at regular intervals. To construct such ribs, concrete is made between such spacings, and the slab is also generated in this fashion, and the slab forms the flange of the T beam.
![]() | ![]() | ![]() |
---|---|---|
![]() |

WAFFLE SLAB
The method was developed to minimize the weight of traditional full-concrete slabs. The dome-shaped geometries create a matrix of voids surrounded by orthogonal ribbing, resulting in a two-way configuration that is appropriate for large-spanning slabs. Because the breadth of that portion of the slab is less than that of a flat slab, voids between all of the domes lessen the dead load. Waffle slabs get their name from their resemblance to waffles with rows of beams running beneath them. Waffle slab illustrates a ceiling that is appropriate for putting all electrical appliances and can give a better view, therefore increasing the aesthetic component.
![]() | ![]() | ![]() |
---|
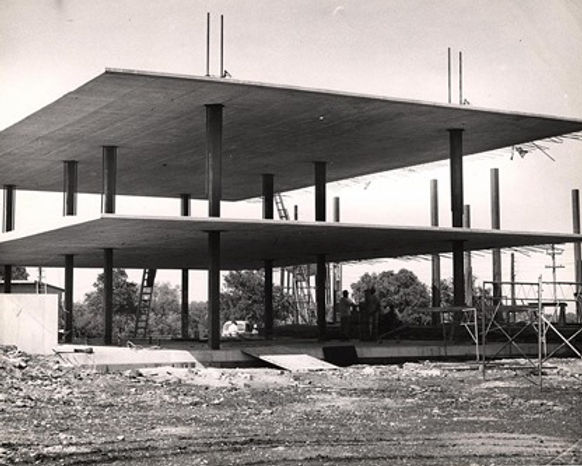
LIFT SLAB
Lift slab construction is a method of building multi-story structures that includes placing multiple concrete slabs on the ground and then lifting these slabs to their assigned, intended altitudes. The lift slab method entails the installation of steel columns that are supported by concrete footings and piers. The slabs are then created around these steel columns, with bond breaker membranes put between each slab cast on the ground and raised with hydraulic jacks.
![]() | ![]() | ![]() |
---|
SPAN STRESS FLOOR SYSTEM
Uses span-stressed pre-stressed T-joists that can be used with filler blocks, foldable steel forms, or plywood forms because the concrete was poured monolithically and is attached to the structure by providing connection reinforcement that transfers lateral forces to the lateral load resisting components
![]() | ![]() |
---|

SLIP FORM METHOD
In theory and application, it is comparable to a jump form, except the formwork is hoisted vertically in a continuous process. It is a method of vertically extruding a reinforced concrete segment suitable for constructing core walls in high-rise constructions such as elevator shafts, stairwells, and skyscrapers. It is a self-contained formwork system that may be constructed with little crane time. This is a formwork system that may be used to make any regular shape or core. The formwork rises at a steady rate of roughly 300mm each hour, supported by the core and requiring no assistance or access from other parts of the building or permanent works. The formwork typically comprises three platforms.The higher platform serves as a storage and distribution space, while the primary working platform is located at the top of the poured concrete level. The lower platform allows for concrete finishing.
![]() | ![]() | ![]() |
---|